- Latest: Welcome to Auto Futures - Mobility News, Features, Exclusives and More...
- Latest: Kia Corporation Unveils EV4 & Concept EV2 at EV Day in Spain
- Latest: Volklec Announces Plans to Open a Dedicated 10GWh UK Battery Gigafactory
- Latest: Mercedes-Benz Begins Solid-State Battery Road Tests
- Latest: BMW Unveils Sixth-Generation BMW eDrive Technology for the Neue Klasse
- Latest: Recovering Critical Battery Materials - Ace Green Recycling CEO
Carbon Hybrid Wheels That are Lighter & More Durable Than Traditional Wheels - Dymag CEO
Adrian Smith
- Nov 01 2022
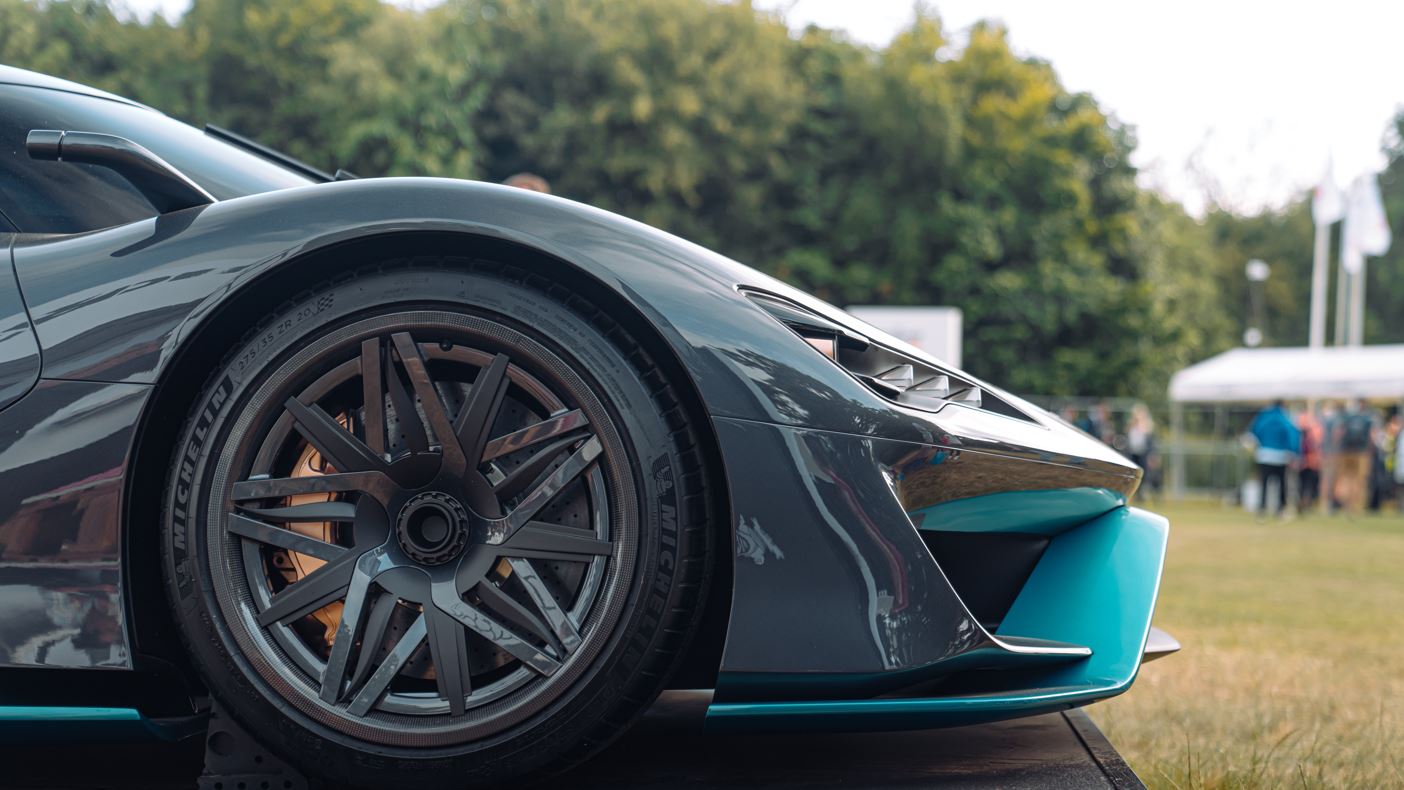
The UK's Dymag has been designing wheels since 1974. It's now developed carbon hybrid wheels that are lighter, stiffer and stronger than traditional cast alloy wheels. They offer major advantages to most vehicles, but particularly the high-performance sector. They also help increase range for electric vehicles (EVs).
Tom de Lange, Dymag's CEO, has been talking to Auto Futures.
Dymag’s carbon hybrid design blends a carbon fibre barrel (the outer section) with a metallic centrepiece (the inner section).
"By using carbon in areas that have the most impact on the inertia of the wheel, and high strength forged aluminium or magnesium in the spokes (where carbon is less optimal due to the compressive forces experienced during normal operation and particularly under impact) the wheel is more than 50% lighter than a traditional alloy, but also stronger and more durable," says de Lange.
Further advantages come in terms of less energy required to accelerate and brake the wheel, and the lightness of the rim itself, which means less steering effort is required.
"These gains can make a huge difference on any vehicle, but for high performance electric vehicles, whether sports cars or large SUVs and pickups/trucks, the benefits are even greater; that step-change four-corner weight saving potentially brings range improvements of around 5%, while carbon fibre’s flexibility can also benefit NVH (noise, vibration and harshness) too – a huge boon for any engineer developing an EV where the ICE is no longer masking unwanted noises," he explains.
Factor in the ability to make a wheel more aerodynamic too, and it becomes easy to see why using carbon hybrid wheels make so much sense on EVs.
"The benefits are so great that it is best to look at carbon hybrid wheels as a key part of the EV engineering solution, because by adding them, everything quickly becomes a virtuous circle enabling a smaller battery, lighter suspension and less sound deadening."
For OEMs, there is a further advantage in that wheels are literally a bolt-on product available off-the-shelf from a supplier who has already done all the necessary testing and development in-house.
"It all comes back to vehicle weight. As each year passes, cars generally get heavier, a problem that is made even worse in battery-powered versions, whether we are talking supercars, SUVs or pickups/trucks. There is also a trend towards larger wheel sizes too. Not that long ago, a 20-inch wheel might only have been the preserve of a motor show concept, but now that size is standard on any large SUV with customers demanding 22-inch, 23-inch and even 24-inch rims," he says.
Accelerating Time-to-Market
The Viritech Apricale, a hydrogen-powered hypercar styled by the Pininfarina design house, features Dymag forged magnesium wheel centres. The Apricale was showcased as the Goodwood Festival of Speed, alongside other cars that sported Dymag's advanced wheels.
In a press release, de Lange comments: “Dymag has a long legacy in advanced automotive wheel technology, being the first to commercialise carbon hybrid wheels almost 20 years ago. Our latest carbon hybrid wheels bring significant benefits to all high-end cars, including EVs, minimising weight, optimising performance, and boasting aesthetic advantages too. BAC, Radford and Viritech are some of the most innovative thinkers in the automotive industry and we’re proud to be working in partnership with them.”
So why aren’t more companies choosing to use carbon-magnesium/aluminium wheels for their EVs?
"Right now, a carbon hybrid wheel costs many more than a conventional cast alloy version. Many of our automotive customers are specialist manufacturers of very low-volume high performance vehicles where cost is less of an issue. But adoption will accelerate in the high-performance EV sector for several reasons. Firstly, understanding of the benefits of carbon hybrid technology is growing and OEMs (as well as the aftermarket where Dymag is a leading supplier), are quickly seeing that a lightweight wheel, can bring huge benefits off-the-shelf, with no development costs," answers de Lange.
The cost of its wheel technology is set to come down. The company recently announced a strategic partnership with Hankuk Carbon Co Ltd, manufacturers of advanced composite materials, to enable the mass production of state-of-the-art high-performance carbon composite wheels.
"This combination of unparalleled resources and technical expertise will accelerate time-to-market and enable economies of scale in the manufacturing of carbon hybrid wheels in series production with a focus on a uniquely scalable and localised approach."
An Increased Focus on Vehicle Customisation
Most OEMs don’t develop wheels, just as they don’t develop tyres. Instead, they rely on specialist suppliers, like Dymag, who have many years of experience in the market.
"For most high-volume electric vehicles, such as the average hatchback, a traditional cast alloy will do the job very well indeed - and be manufactured in such numbers that it will be very cost-effective. But for high-performance versions of EVs, whether cars, SUVs or pickups/trucks, which require larger wheels that do a more specific job, then an OEM really needs to ask if a cast alloy wheel is up to the task. Increasingly, that is not the case - and it’s at that point that a manufacturer should turn to a specialist and we believe we have the solution."
As more companies adopt EVs, de Lange says we can expect the industry to increasingly focus on customisation and new means of differentiation.
"It will become increasingly difficult for premium OEMs to distinguish their products from the opposition and to justify the cost of top end, high margin models in their range. They no longer have the distinguishing factor of an amazing V8 versus 4 cylinder engines further down the range; even the lower end electric cars will accelerate quicker than most people need, so having something even quicker will become increasingly irrelevant over time. So items such as wheels, suspension upgrades, body kits and in-car tech will become increasingly important and carbon hybrid wheels could be an important option for differentiation on high end cars, just as carbon ceramic brakes are currently."
Finally, we asked de Lange how he sees driving changing over the next ten years.
"With the ban on new sales of petrol and diesel cars in 2030, there is clearly going to be a big shift as electric vehicles become the norm for most of us. But there will always be enthusiasts who want to enjoy driving, no matter the powertrain," he says.
"This may well mean that the last of the petrol-powered sports cars and supercars become revered as the peak of the combustion engine and continue to be enjoyed on a weekend basis on the public road - or maybe even limited to just private test tracks (depending on where you live in the world and your country’s attitude to emissions)."
"As everything starts to become more regulated and automated, there is likely to be an increase in the focus on customisation of vehicles: just witness the huge modifying scene within the Tesla community for instance. That is only likely to grow. For all these audiences, wheels will become even more of a key component, whether through the desire to stand out through increased visual impact or improved performance. Or both! If you can make your supercar handle really nicely and not be too heavy, then you will stand out in the marketplace," predicts de Lange.
Popular Categories