- Latest: Welcome to Auto Futures - Mobility News, Features, Exclusives and More...
- Latest: Kia Corporation Unveils EV4 & Concept EV2 at EV Day in Spain
- Latest: Volklec Announces Plans to Open a Dedicated 10GWh UK Battery Gigafactory
- Latest: Mercedes-Benz Begins Solid-State Battery Road Tests
- Latest: BMW Unveils Sixth-Generation BMW eDrive Technology for the Neue Klasse
- Latest: Recovering Critical Battery Materials - Ace Green Recycling CEO
Cheaper, Safer and Cleaner - How Sakuu's 3D Printed Batteries are Shaping Future Manufacturing
Lynn Walford
- May 24 2023
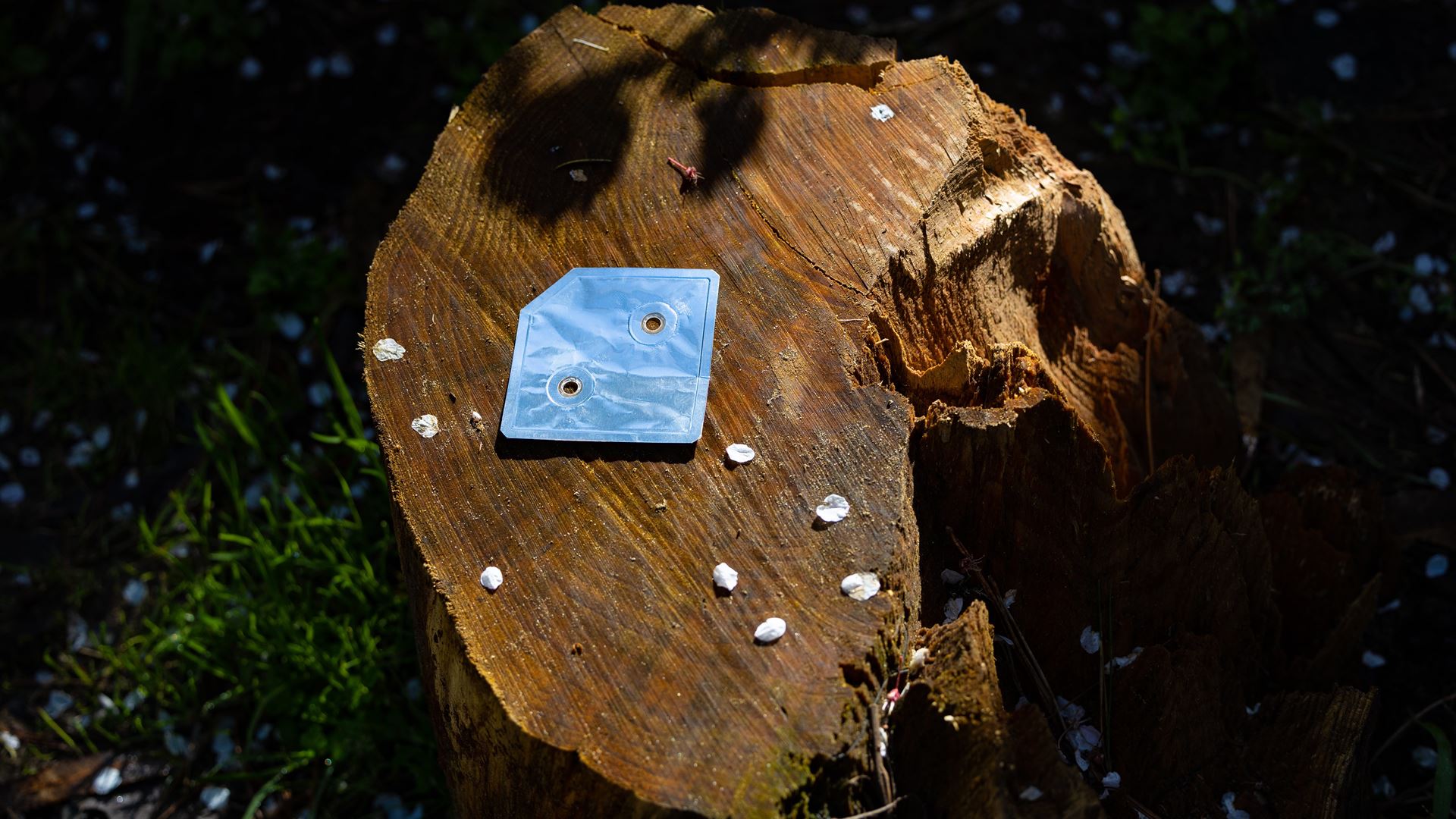
The 3D printing process from Sakuu is changing the shape of batteries and the manufacturing. Arwed Niestroj, SVP E-Mobility and Product at Sakuu, details the advantages of the Kavian additive manufacturing platform for next-generation 3D SwiftPrint batteries and other devices.
The Form And Function of 3D Batteries
The main advantages of 3D printing are reduced cost, sustainability, faster charging, safety (non-flammable), higher density and custom shapes, says Niestroj. For sustainability, the process uses less material and creates waste. The dry process is more cost-efficient and more sustainable.
He says that additive printing manufacturing allows for thinner layers of most of the layers in the battery. In fact, California-based Sakuu estimates that compared to Li-ion batteries, SwiftPrint cells are 30% smaller and 40% lighter on average - with twice the energy density. And the batteries can be made in any shape.
"When you make batteries by 3D printing, the batteries do not have to be cylindrical or rectangular anymore. They can be any shape. They can fill the space that you provide for them. You can design the battery into the product and not the product around the battery," explains Niestroj.
He gave the example of a virtual reality headset.
Efficient Batteries With Cool Holes Without Tabs
He showed an odd-shaped battery with holes in it.
"You can create new solutions for cooling the thermal management of batteries by putting a hole in the battery, right where most of the energy in the heat is generated," says Niestroj.
Sakuu developed a 3D printing press that uses multiple processes, not only one 3D printing process but different ones in different stations and the material moves to the printer - making it fast, he adds.
"3D printing is fast, cheaper using phase material, a dry process, and gets much better control of the important features of a battery, including layer thickness, interface quality, performance shape, and sealing the battery in the printer."
The Kavian 3D printing process can make conventional lithium-metal liquid electrolyte batteries and solid-state batteries. The process has less operational expenditures and a lower energy cost than a conventional rotor-roll coating process, he added.
The Sakuu batteries do not require tabs. The conducting surface and outer surface are the same, so they can be stacked on top of each other and connected with wires connecting all the bands together.
"Printed batteries allow you to control the interface and behaviour of lithium in the anode and the cathode, which provides much more efficient thermal management, which means more energy and longer range in electric vehicles," says Niestroj.
How Are 3D Batteries Manufactured?
The founders of Sakuu have several decades of experience in semiconductor manufacturing and started applying the same technology to batteries combining additive manufacturing with material science so that the material can be printed, and applied to batteries, he explained
"The equipment is made by manufacturing partners, and the process will be fully automated. The material will be supplied as a raw material to the printer, and then out comes to the battery fully made," says Niestroj.
AI and machine learning are used in the additive manufacturing process. The customer can specify the shape of the battery, and the software optimizes how the forms and shapes are used in the printer.
Sakuu is targeting high-energy and high-power applications with the current battery such as electric two-wheelers. Also, Sakuu is working on batteries for aerospace, home-energy storage and other industries. The process can make batteries for power tools, tactical radios and drones.
What Else Can Kavian Do?
The Kavian platform can print other devices, like antennas, 5G antennas or Wi-Fi antennas, and medical devices, at a much lower cost than the processes used today, which typically is a semiconductor process, says Niestroj.
The process can be used to make PCR tests, pathogen detection, biometric sensors or other medical devices.
"The manufacturing approach that has been used for decades to make batteries, to provide more energy be safer and flexible, has to be changed. We're the only ones doing it. That is what enables new advantages to be generated. It is reinventing manufacturing."
"We are ready to license our manufacturing process. We are talking to partners to build factories, and we have first agreements with partners who will build factories using our equipment," he reports.
He notes that changing the battery shape and manufacturing process will change the industry.
"Additive -manufacturing not only changes the shape of batteries but re-shapes the industry and how batteries are made. These new battery factories will look different in five years," Niestroj predicts.
Popular Categories