- Latest: Welcome to Auto Futures - Mobility News, Features, Exclusives and More...
- Latest: Kia Corporation Unveils EV4 & Concept EV2 at EV Day in Spain
- Latest: Volklec Announces Plans to Open a Dedicated 10GWh UK Battery Gigafactory
- Latest: Mercedes-Benz Begins Solid-State Battery Road Tests
- Latest: BMW Unveils Sixth-Generation BMW eDrive Technology for the Neue Klasse
- Latest: Recovering Critical Battery Materials - Ace Green Recycling CEO
Crash Testing Cars on Computers — Monolith AI founder and CEO Dr Richard Ahlfeld
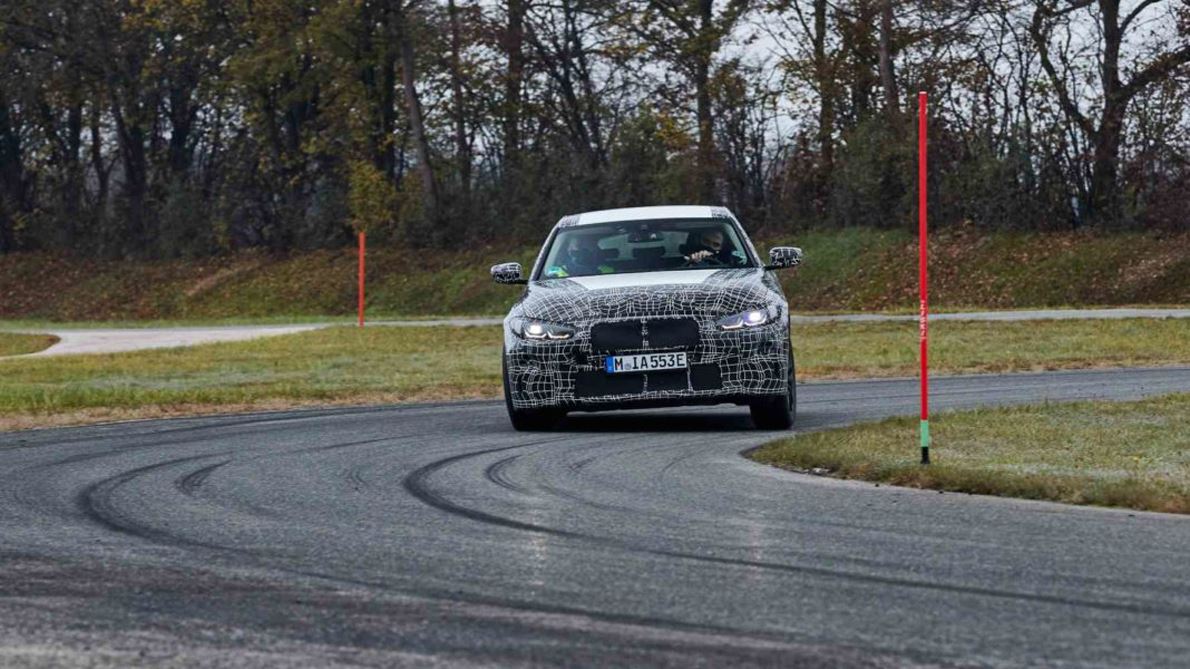
“When I founded Monolith, I was a Fellow for Machine Learning at Imperial College London, working, among other things, on the NASA Mars rocket,” says Dr Richard Ahlfeld, the company’s CEO.
You don’t often get to speak to someone who has helped put a rocket into space. It’s even rarer that the same person is now working with BMW to make its cars safer and the Jota Le Mans team to make its cars quicker.
In fact, thanks to Monolith’s machine learning, BMW’s cars are being prepped for crashes that could never be simulated in the real world, and Jota’s cars are being pushed to the limit without needing to turn a wheel.
Virtually Reality
“My background is in academia and research and a lot of my time at London Imperial College was spent looking at how data science techniques could be applied to the field of engineering,” continues Ahlfeld.
“It was clear for me that deriving insight from data for decision-making is a complex but necessary challenge for engineering organisations. Engineers understand the data, they are embedded in the business, and have the intuitions necessary to know why to process and model data.”
However, while engineers can build models and simulations to test their products, the process can be lengthy.
“As an engineer, you may have been tasked with building a model and then using that model to virtually design the perfect product with the hope that the physics-based simulation approach will do its job,” says Ahlfeld.
“But what I’ve found in the industry is that if you want to radically accelerate the speed of developing a new product, you need a radically different solution to understand the physical challenges that are still not fully understood.”
Accelerating the testing process, though, is only one part of Monolith’s work.
“Monolith empowers engineers to use AI to solve their most intractable physics problems. We do this by enabling engineers to use their existing data from the current product development process,” explains Ahlfeld.
“They can then build self-learning models that can instantly predict results for challenges that would otherwise have to be solved using extensive, time-intensive physical testing. These self-learning models learn from existing data and identify patterns to solve challenges that until now, have been beyond the scope of what the human engineer or simulation technology can do.”
By using massively advanced machine learning, but having a no-code interface, Monolith lets engineers and companies solve incredibly complex problems quickly.
Engineers at the Honeywell corporation, for example, were using Computational Fluid Dynamics to understand gas fluid dynamics when developing a smart gas metre.
“But the simulations weren’t 100% accurate,” says Ahlfeld, “leaving a critical gap in understanding between simulation and reality. Using Monolith, the engineers are using statistical machine learning methods to close the gap, allowing them to instantly and accurately understand the impact of varying temperature conditions and types of gases across all operating conditions, including extreme and unsteady parameters.”
Simulating the Impossible
“When faced with intractable physics problems, engineering domain experts can use Monolith to immediately leverage their existing data and instantly solve the previously unsolvable and in doing so, get back literally weeks or months of their time,” says Ahlfeld.
BMW has been using the software to simulate crash tests with impressive accuracy.
“A crash test is a highly non-linear, expensive undertaking that heavily relies on traditional R&D methods using thousands of simulations as well as numerous physical crash tests to capture vehicle performance and ultimately fulfil global homologation requirements, rightly so,” says Ahlfeld.
“But even with sophisticated modelling techniques, owing to the complexity of the physics underpinning crash dynamics, results require substantial engineering expertise to calibrate for the real world. Moreover, physical crash tests can only be conducted in later stages of development when the design is mature enough to create physical prototypes.”
Monolith started working with BMW in 2019 and Ahlfeld says that the simulations will only continue to improve.
“The engineers built self-learning models using the wealth of their existing crash data and were able to accurately predict the force on the human tibia for a range of different crash types without doing physical crashes,” Ahlfeld explains
“In future, the accuracy of the self-learning models will continue to improve as more data becomes available and the platform is further embedded into BMW’s engineering workflow. This means engineers can optimise crash performance earlier in the design process and reduce dependence on time-intensive, costly testing whilst making historical data infinitely more valuable.”
The Jota racing team are also seeing a range of benefits from using Monolith’s software.
The #38 Jota Sport car that finished first in the LMP2 class at the Le Mans 24 Hours
“Jota is using Monolith to accelerate their design and engineering processes in every area of engineering from car setup, vehicle dynamics, aerodynamics and tyre degradation modelling,” says Ahlfeld.
“By incorporating Monolith within real-time testing, Jota engineers reduced the number of simulations and tests by 50% and associated costs by 66%, making faster, better design decisions and streamlining how car and simulation data is validated.”
Accelerating Change
Of course, while AI testing is great for simulating events at the fringes of possibility, Ahlfeld believes that the real benefits in the years to come will be in the pace of development.
“No matter what new technology is introduced, be it autonomous, connected or electric, engineers will always need to create a fundamentally great car to stay competitive and drive demand — from premium acoustics and greater fuel efficiency to safety and vehicle dynamics,” he says.
“AI technology can radically transform vehicle development by empowering engineers to extract the best possible insights and predict results from existing engineering data, and much earlier in the development process. This allows engineers to arrive at design and engineering decisions quicker and more efficiently, giving them time to explore even more design parameters and operating conditions.”
“Ultimately this means OEMs can bring better vehicles to market faster which isn’t just vital to reach our collective EV ambitions but allows engineers to do what they love best — engineering incredible products.”