- Latest: Welcome to Auto Futures - Mobility News, Features, Exclusives and More...
- Latest: Kia Corporation Unveils EV4 & Concept EV2 at EV Day in Spain
- Latest: Volklec Announces Plans to Open a Dedicated 10GWh UK Battery Gigafactory
- Latest: Mercedes-Benz Begins Solid-State Battery Road Tests
- Latest: BMW Unveils Sixth-Generation BMW eDrive Technology for the Neue Klasse
- Latest: Recovering Critical Battery Materials - Ace Green Recycling CEO
How Cyclic Materials is Creating a Circular Supply Chain for Rare Earth Elements - CEO Ahmad Ghahreman
Breanna Sherman
- May 30 2023
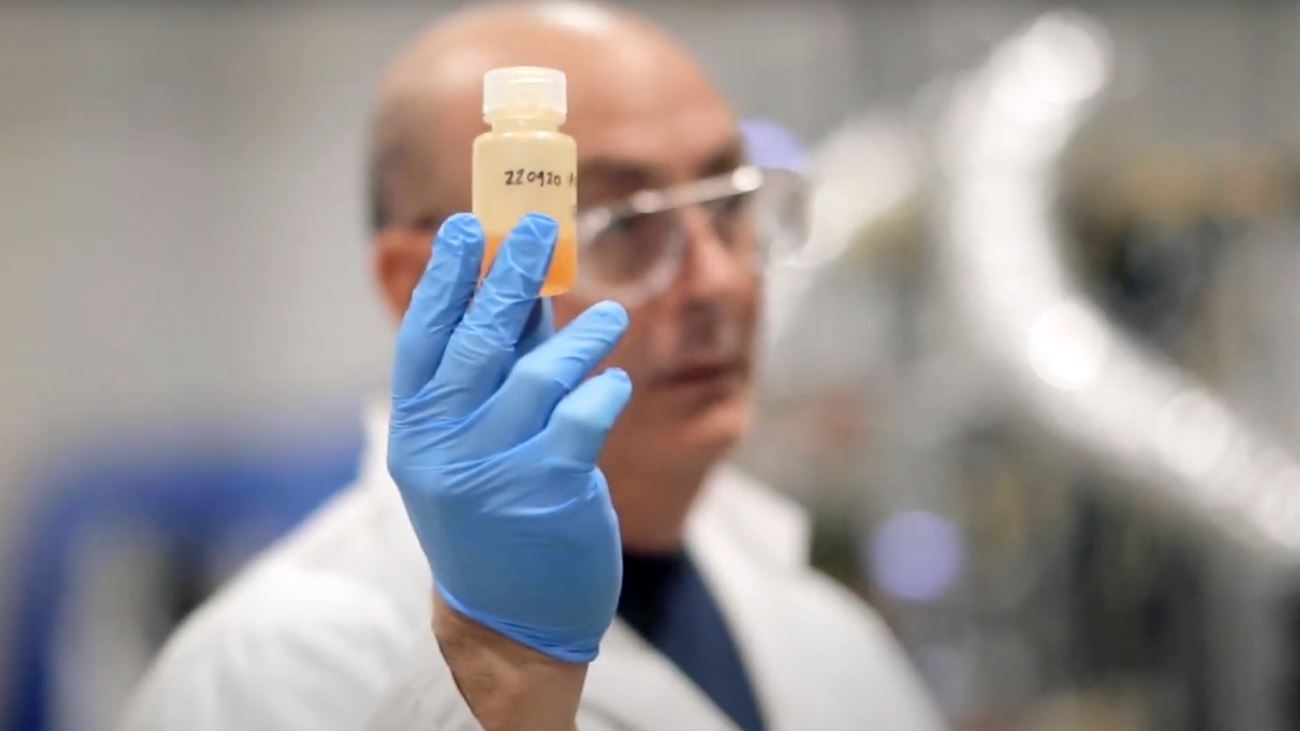
Rare earth magnets are made from alloys of rare earth elements (REEs) and their incomparable strength has led them to become vital components of electric vehicle (EV) motors and wind turbines. The problem is that EV motors are not necessarily designed to be fully recycled, despite the environmental impact that occurs in mining these elements.
As a result, the recycling of these materials is virtually non-existent; they are simply tossed into the landfills of steel-making plants.
However, for Cyclic Materials' CEO, Ahmad Ghahreman, this was, “hard to see and ignore, and not do anything about it.”
Ghahreman has been talking to Auto Futures.
A Necessary Circular Supply Chain
When an EV motor is no longer viable, and its materials are grinded up, there is a separation of elements such as copper, aluminum, and steel. However, its REE magnets are not separated in the same way. Instead they attach to the motor’s steel. When this steel gets recycled, it becomes slag, and the rare earth metals become waste.
The solution? Cyclic Materials has created an innovative process that allows for the recovery and recycling of these magnets.
“By no means does Cyclic Materials claim that they’re going to stop mining of rare earth elements. We are not… All Cyclic Materials is able to do, is reduce the pressure on the need for mining of these metals. So, the more of those metals we recycle, the less mining would be required to happen in the world,” explains Ghahreman.
The reduced environmental impact should be incentive enough, but the addition of recycled rare earth magnets to the market will also reduce supply chain insecurities.
The market is already experiencing a deficit in the availability of rare earth metals, and this will only worsen in the next 10-15 years. Ghahreman explains that “the metals [they] will recycle and put back into the market will be part of the solution to fast-track our movement towards electrification.”
Cyclic Materials’ Technology
The company has two pieces of technology that allow for environmentally low-impact recycling of magnets. The first technology allows for the separation of the magnets from the motors, and the second technology allows for these isolated magnets to then be converted to raw materials.
“The technology enables us to… recycle the magnet materials and convert it to the raw materials that then you could use to produce or manufacture brand new magnets, or use the chemicals, reagents in other applications, whatever the market needs,” explains Ghahreman.
Copper, aluminum, and cobalt are a few of the metals that Cyclic Materials recycles, among several others that are globally considered to be critical minerals. The company is creating a circular supply chain. End-of-life products are transformed into valuable raw materials, and it does so domestically, economically, and sustainably.
“When you recycle these metals… you make those available to the downstream industry, with far, far less environmental impact,” says Ghahreman.
A Growing Need For Magnets
Mining REEs is costly and damaging to the environment. The extraction process can cause erosion, pollute the air, contaminate water resources, and it leaves behind toxic waste. However, global demand for REEs is set to skyrocket by 400-600 per cent over the next several decades.
“With electrification, with robust sales of EVs, with robust installations of wind turbines, the need for magnets is increasing every day,” explains Ghahreman.
According to the IEA’s Global EV Outlook 2023, there were 26 million electric cars on the roads globally in 2022, which is a 60% increase from 2021. Recycling rare earth magnets may not have been a relevant endeavour in the past, but it is essential for a “green” energy transition.
“There is a bottleneck in recycling of critical metals that we normally use in the electric motor of electrified products,” says Ghahreman.
He credits the conception of Cyclic Materials to his, “passion for recycling and understanding of the industry put together with the excitement of how fast electrification is happening in our society.”
Big Plans For Cyclic
The company has just raised Series A funding worth USD$27 million. The round was led by BMW i Ventures (BiV) and Energy Impact Partners (EIP). It will be used to scale up and advance the company’s technologies, with plans to prepare it for commercial installation. For the time being, these build outs will happen in Ontario, Canada.
In a BMW i Ventures press release, Managing Director Kasper Sage, states: “The Cyclic team has developed a novel process that can create a sustainable, secondary supply source. We are excited for the company's plan to scale this technology, helping secure the metals supply chain of the future.”
“The funding from BMW I Ventures, and Energy Impact Partners… will be very helpful in advancing our technology in the next round and I think that’s the part we are most excited about,” concludes Ghahreman. “We are not planning small things here.”
Popular Categories