- Latest: Welcome to Auto Futures - Mobility News, Features, Exclusives and More...
- Latest: Kia Corporation Unveils EV4 & Concept EV2 at EV Day in Spain
- Latest: Volklec Announces Plans to Open a Dedicated 10GWh UK Battery Gigafactory
- Latest: Mercedes-Benz Begins Solid-State Battery Road Tests
- Latest: BMW Unveils Sixth-Generation BMW eDrive Technology for the Neue Klasse
- Latest: Recovering Critical Battery Materials - Ace Green Recycling CEO
How Li-Cycle is Recovering Critical Materials From Lithium-ion Batteries - Regional President, EMEA, Richard Storrie
- Jul 24 2023
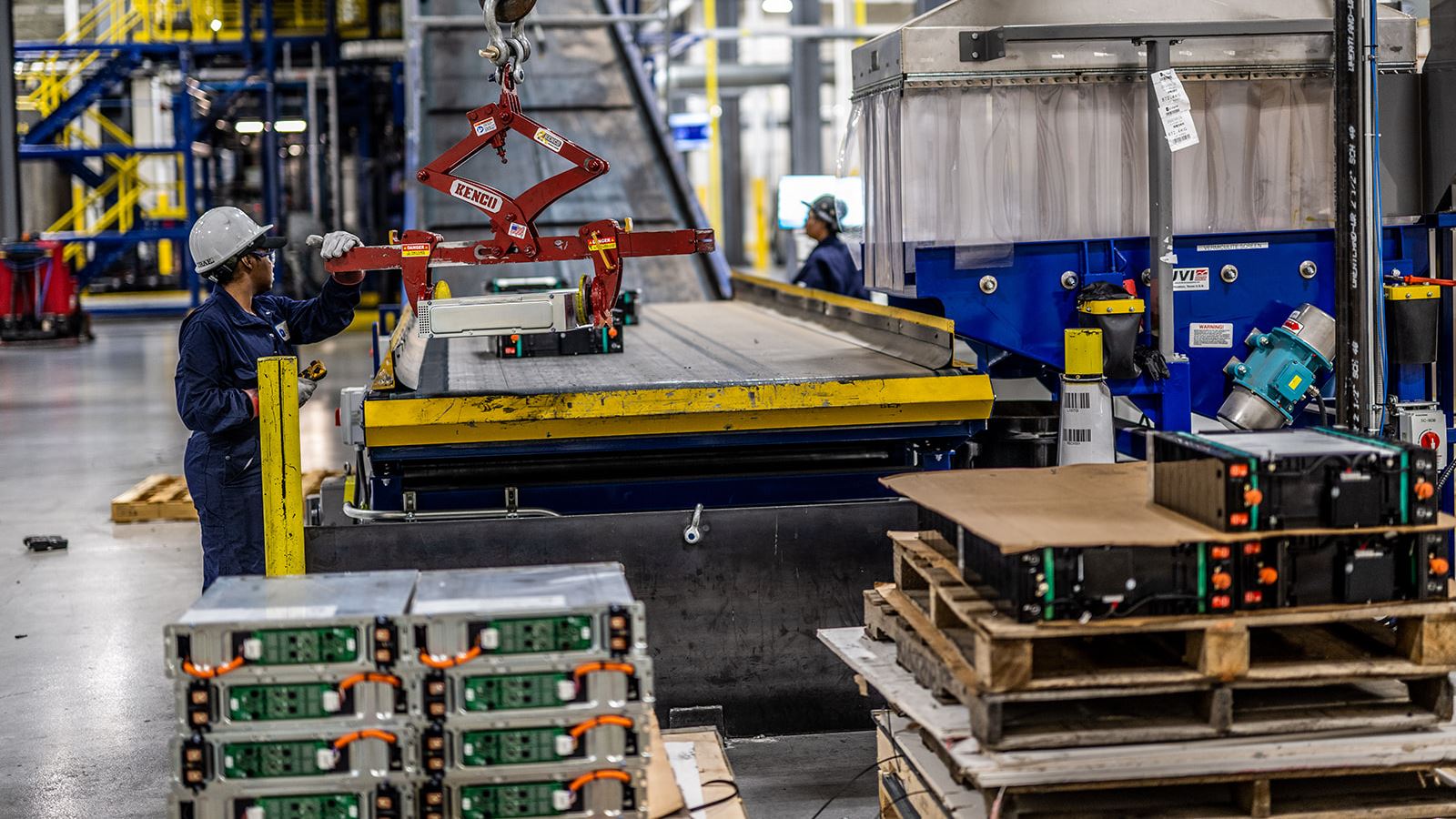
Canada's Li-Cycle was founded in 2016 to address a missing link in the future of global electrification – the lack of an economically and environmentally sustainable lithium-ion battery recycling solution. Fast forward to today, its technologies are returning lithium-ion batteries and battery manufacturing scrap to the supply chain with up to a 95% recovery rate.
"As Li-Cycle scales its industry-leading technologies, we maintain an unwavering dedication to sustainability. The paramount focus remains on minimizing solid waste streams, reducing wastewater discharge, and mitigating the impact of air emissions," Richard Storrie, Li-Cycle’s Regional President, EMEA, tells Auto Futures.
Li-Cycle's Spoke & Hub Technologies business model enables the return of battery materials back to the domestic supply chain for re-use by battery manufacturers and electric vehicle (EV) and energy storage producers.
At the company's Spokes facilities battery materials are recycled through a shredding process to produce ‘black mass,’ an intermediate product which contains highly valuable metals, including lithium, nickel, and cobalt.
"Our Generation 3 Spoke technology has the capability to directly process full electric vehicle (EV) and energy storage battery packs without any manual dismantling or discharging, which enhances safety and efficiency and is a significant value differentiator for Li-Cycle. Our Spoke technology is also one of the most energy efficient solutions commercially available," explains Storrie.
"Across our operational Spokes in North America, we have a total processing capacity of 51,000 tonnes of lithium-ion battery material per year. While we have predominantly been expanding and bolstering our presence in North America, with the majority of our recycling capacity within the U.S," he adds.
Its first European Spoke has now commenced operations in Magdeburg, Germany, which is also its largest Spoke to date.
"We have other European Spokes planned in Norway and France, which will bring Li-Cycle’s future planned capacity across our global Spoke network to more than 100,000 metric tons of lithium-ion battery material per year," says Storrie.
The Challenges Of E-Waste
At Li-Cycle's Hub facilities, the 'black mass' is processed to produce battery-grade materials, or the fundamental building blocks of batteries, such as lithium carbonate, nickel sulphate, cobalt sulphate and manganese carbonate.
Its first commercial Hub facility is under construction in Rochester, New York, and is on track to commence commissioning in late 2023 with a ramp-up of operations in 2024.
"Once fully operational, the Rochester Hub is expected to deliver annual production of up to 7,500-8,500 metric tons of battery-grade lithium carbonate, 42,000-48,000 metric tons of battery-grade nickel sulphate, and 6,500-7,500 metric tons of battery-grade cobalt sulphate, in addition to other valuable materials. This Hub is expected to be one of the largest sources of lithium supply in North America and will be able to process the equivalent of approximately 300,000 EVs worth of lithium-ion battery material per year," says Storrie.
The facility is expected to be the first source of recycled battery-grade lithium carbonate in North America.
"It is a flagship asset for our business, but we also strongly believe this first-of-its-kind clean-tech refining facility will play a key role in solving many challenges associated with e-waste across North America and Europe."
Recycled Battery-Grade Lithium in Europe
Li-Cycle joined forces the natural resources giant Glencore in 2022 to drive circularity in battery raw material supply chains. Previously Glencore had invested $200 million in the company. They recently announced an expansion of their strategic partnership.
"Through a planned 50-50 joint venture, Li-Cycle and Glencore plan to study the development of a Hub in Portovesme, Italy. The Portovesme Hub would be a landmark project for Europe’s battery recycling industry and is expected to be the largest source of recycled battery-grade lithium, as well as recycled nickel and cobalt, on the European continent," says Storrie.
"To align with our recycling expertise, we plan to repurpose an existing Glencore metallurgical facility to enable a cost-efficient and expedited development plan. Once operational, the Portovesme Hub is expected to have a processing capacity of the equivalent of approximately 600,000 EVs worth of lithium-ion batteries," he adds.
Finally we asked Storrie what EV battery recycling will look like by the end of the decade.
"In 2023, Li-Cycle expects that approximately 290,000 metric tons of battery material will be available for recycling compared to only 34 thousand metric tons of post-processing capacity in North America. By 2030, Li-Cycle expects that that there will be approximately 1 million metric tons of material available for recycling, or a three-fold increase, compared to less than 400,000 metric tons of post-processing recycling capacity. This growth will predominantly be driven by manufacturing scrap," he predicts.
Popular Categories