- Latest: Welcome to Auto Futures - Mobility News, Features, Exclusives and More...
- Latest: Kia Corporation Unveils EV4 & Concept EV2 at EV Day in Spain
- Latest: Volklec Announces Plans to Open a Dedicated 10GWh UK Battery Gigafactory
- Latest: Mercedes-Benz Begins Solid-State Battery Road Tests
- Latest: BMW Unveils Sixth-Generation BMW eDrive Technology for the Neue Klasse
- Latest: Recovering Critical Battery Materials - Ace Green Recycling CEO
Racing Ahead With Design, Simulation And Manufacturing – Team Rosberg Engineering (TRE) in Focus
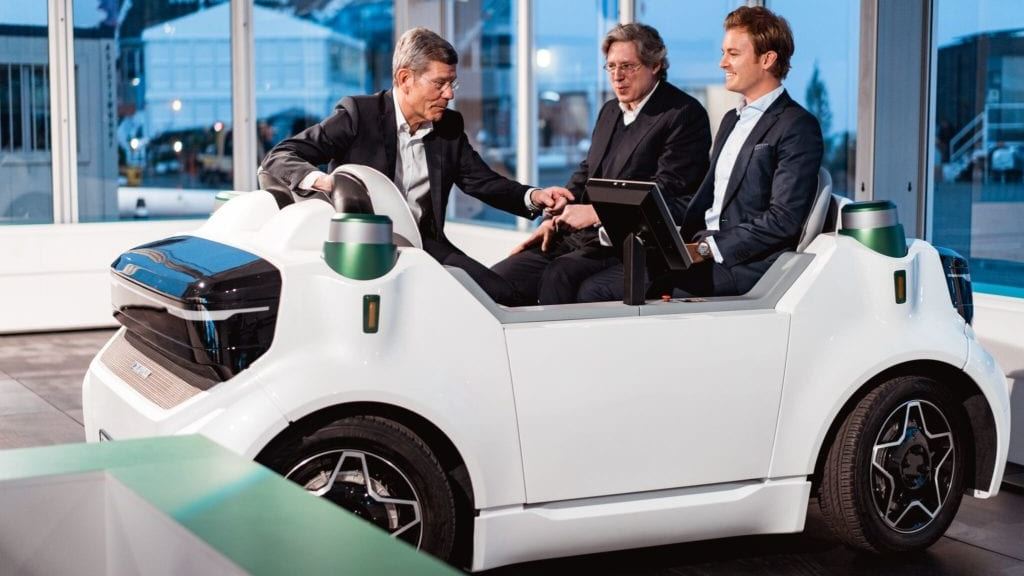
Not every mobility company has a Formula 1 world champion as an investor. But the clue is in the name. TRE stands for Team Rosberg Engineering. It was established in 1997 by Keke Rosberg. He had the idea of establishing a centre for the series development of chassis components alongside the racing team.
The racing engineers were able to make their expertise in chassis development and tuning available to major car manufacturers. Today, Keke’s son, Nico Rosberg, who won the Formula 1 World Championship in 2016, is an investor in the company.
Auto Futures has been talking to Stephan Müller, Head of Business Development at TRE GmbH and Axel Hoffmann, Head of Chassis Development.
“Since 2008, we have been a joint venture between the Team Rosberg racing team and IAV GmbH. IAV is based in Berlin and employs more than 8,000 people worldwide. This partnership enables us to draw on the resources of one of the world’s leading development partners to the automotive industry in Europe, America and Asia for many projects, offering our customers holistic development scopes and first-class expertise from a single source,” says Müller.
From concept through to design, simulation and testing, TRE has offers its customers all steps of a chassis development from a single source.
“Starting with the legendary white sheet of paper, we develop individual chassis concepts for test vehicles, concept vehicles and series production projects. We define promising development approaches with the help of initial numerical simulations and computer-aided design (CAD) structural analyses. In addition to classic axle designs, we develop completely new chassis concepts that are specifically adapted to innovative drive concepts and vehicle architectures. TRE thus makes a major contribution in the field of future mobility,” Müller explains.
In terms of design, TRE creates 3D models and drawings using CAD software.
“We design components suitable for production and assembly, depending on the area of application. In addition to primary forming, reshaping and conventional shape cutting, we also design components for additive manufacturing (metal 3D printing). The design is carried out in close coordination with our long-standing suppliers (from manufacture to Tier1). Thanks to our network, we can also provide high-quality hardware at short notice.”
The company’s engineers use TRE’s own state-of-the-art development tools for chassis simulations.
Müller goes on to explain prototype production, and finally, the testing process. “From single pieces to small series, we provide production in our in-house workshop. With great expertise in welding technology, we produce welded assemblies from steel, stainless steel and aluminium – from simple sheet metal brackets to steering arms and axle carriers to complete tubular vehicle frames. We adapt series parts for use in prototypes. We also handle the necessary Jig making in-house.”
“Our experts deal with all facets of vehicle dynamics. Using extensive, in-house measuring technology such as steering and braking robots, they carry out homologation-relevant and manufacturer-specific tests. As part of the application, they tune the parameters for the electronic control systems as well as for spring, damper and steering systems,” says Müller.
TRE’s experts are also able to assess driving dynamics and ride comfort on the basis of customers’ driving manoeuvre catalogues or TRE’s own specification.
TRE in the Driving Seat
After winning the Formula 1 World Championship, Nico Rosberg ended his racing career, which he had started with Team Rosberg, among others. He’s been involved with TRE since 2018. In 2019, Rosberg founded the GREENTECH FESTIVAL, a global platform to showcase pioneering green technologies.
In 2021 his own team – Rosberg Xtreme Racing (RXR) – made its racing debut in Extreme E, the new electric off-road racing series.
“Nico Rosberg has been active as a sustainability entrepreneur and investor, with a strong focus on mobility companies. He is driven by the ambition to promote positive change for society and humanity by fostering innovation and technological progress. Under this maxim, he is an investor in a number of successful start-ups. TRE also benefits from these inspirations,” says Müller.
At CES 2019 in Las Vegas, Rosberg was able to present an autonomous vehicle concept innovation, developed with Schaeffler, in person.
“In cooperation with Schaeffler Paravan Technology GmbH & Co. KG we were involved in the development of the small, very maneuverable and electrically driven vehicle concept Schaeffler Mover. It uses Space Drive technology, which allows the vehicle to move autonomously. Automatic lane guidance, steering, braking and acceleration are controlled by electrical impulses. On behalf of Schaeffler Paravan Technology, we developed the revolutionary Corner Modules, which allow the vehicle to park sideways and turn on the spot,” explains Müller.
Supporting Sono
TRE has also been supporting the Munich-based start-up SonoMotors in the selection of a suitable axle concept for its Sion vehicle project. In January 2021 the two companies announced a closer cooperation. TRE, is now also responsible for the production of the chassis prototypes (axle modules).
“For the up-and-coming car manufacturer SonoMotors, our ‘out of one hand philosophy’ makes us an ideal partner for the complete suspension and chassis system for such an innovative project. In detail, this collaboration looked like this: From computer model to finished axle. Computer work is indispensable for the development of vehicle parts. With the help of CAD models, engineers design the various components and assemble them. Many different factors have to be taken into account in the process,” explains Müller.
“The scope at TRE is divided into the areas of design, simulation as well as manufacturing,” says Axel Hoffmann, Head of Chassis Development at TRE. “In the design team, the chassis is laid out and the new components are designed, making the best possible use of the available installation space.”
“We designed more efficient prototype manufacturing processes for parts such as subframes, wheel carriers, stabilizer bars and composite control arms, which are produced in high volumes in series using expensive tooling. The properties and functions of the prototype parts designed in this way already largely correspond to those in the production vehicle – despite the fact that no production tooling is used. This means the vehicles can be used for fine-tuning runs and road tests,” adds Hoffmann.
Electric drive and other drive concepts such as hydrogen will characterize the mobility of the future.
For TRE, the increasing electrification of the vehicle fleet opens up completely new approaches for chassis development.
“The current weight distribution (engine in the front) is changing in such a way that in the future the heavy batteries will be installed under the footwell of the vehicles. This results in a change in the centre of gravity. The elimination of the combustion engine also means that this area offers new installation space that can be used individually,” says Müller.
Looking further ahead, we quizzed Müller on what mobility will look like by the end of the decade.
“Mobility will change fundamentally in the next 10 years. Electric drive and other drive concepts such as hydrogen will characterize the mobility of the future. Also mobility will change significantly in particular in urban areas. The first early adopters with e-scooters, autonomous shuttles, L7e vehicles, car-sharing, e-bikes and cargo bikes already indicate this trend. Individual vehicles will also undergo a major transformation.”
“Autonomous driving and steer-by-wire are just a few buzzwords in this context. Airspace will also open up more and more to individual transportation. We will increasingly encounter air cabs for passenger transport and drones for the last mile of parcel delivery in the future,” concludes Müller.